Why More Factories are Using Aluminum Framing for Modular Work Tables in Lean Manufacturing
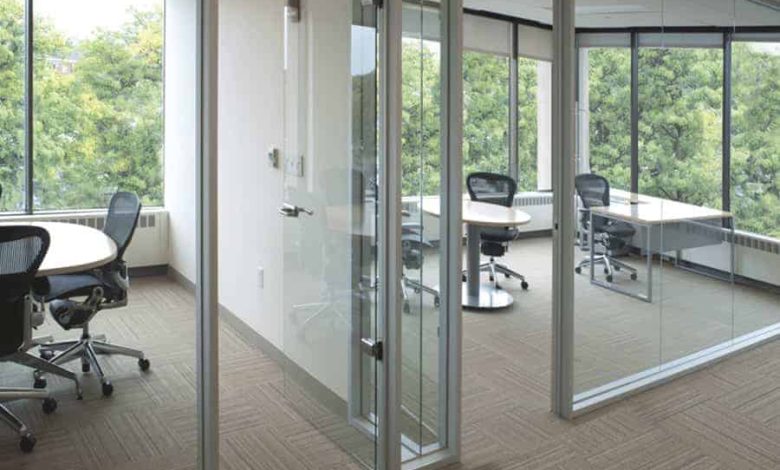
Factory floors never stay the same for long. As production demands shift, businesses need workstations that can keep up without costly downtime or major overhauls. That’s why more manufacturers are turning to modular work tables built with aluminum framing—offering flexibility, strength, and efficiency for fast-moving production environments.
How Modular Work Tables Adapt to Changing Production Needs
Traditional workstations are often fixed in place, making adjustments difficult when new processes or equipment are introduced. Modular work tables solve this problem by offering a flexible design that can be easily expanded, repositioned, or reconfigured as needed. With aluminum framing, manufacturers can quickly add new components, change table heights, or integrate accessories like shelving and tool mounts without extensive modifications.
This adaptability is especially valuable in lean manufacturing, where efficiency is a top priority. Production teams can reorganize workstations based on workflow demands, ensuring that space is used effectively and workers have what they need within reach. Instead of tearing down and rebuilding stations, factories can modify existing setups, saving both time and money while maintaining a smooth production flow.
Lightweight Frames That Simplify Factory Layout Adjustments
Rearranging a factory floor can be a logistical nightmare when dealing with heavy, cumbersome workstations. Steel-framed tables, in particular, require significant effort and sometimes even special equipment just to move. In contrast, aluminum framing offers a lightweight yet durable solution that makes factory reconfigurations much simpler.
Because aluminum is significantly lighter than steel, workstations can be repositioned without the need for forklifts or extensive labor. This allows factories to quickly respond to shifting production needs, whether it’s creating new assembly lines, optimizing space, or accommodating new machinery. With reduced strain on workers and easier handling, aluminum framing helps keep operations efficient without the hassle of relocating bulky, outdated equipment.
Why Aluminum Holds Up Better Than Traditional Steel in Fast-Paced Workflows
Steel has long been the standard for industrial workstations, but it comes with drawbacks. Over time, steel frames are prone to rust, corrosion, and even warping under continuous stress. Aluminum framing, on the other hand, provides superior durability while remaining resistant to rust and environmental wear, making it a better fit for fast-paced manufacturing environments.
In high-output production settings, workstations need to withstand constant movement, tool impacts, and heavy loads. Aluminum’s natural resistance to corrosion means it maintains its strength and appearance without requiring constant maintenance. Unlike steel, which often needs protective coatings or treatments, aluminum stays strong with minimal upkeep, making it the more practical choice for factories focused on long-term performance.
Faster Assembly and Reconfiguration Without Specialized Tools
Setting up new workstations should be quick and straightforward, but traditional steel frames often require welding, drilling, or heavy-duty tools to make modifications. This slows down installation and adds unnecessary complexity to what should be a simple process. Aluminum framing eliminates these challenges with modular designs that allow for fast assembly and reconfiguration without specialized tools.
Most aluminum-framed work tables use pre-engineered connectors and fastening systems, allowing teams to assemble or adjust them with just basic hand tools. This speeds up installation, reduces downtime, and allows manufacturers to scale production lines with ease. Whether a workstation needs height adjustments, additional storage, or integration with conveyor systems, aluminum framing makes modifications seamless without relying on costly outside labor.
Customizable Workstations That Improve Efficiency and Ergonomics
Not all workstations fit every worker or every task, and a one-size-fits-all approach can hurt productivity. Modular tables built with aluminum framing allow for highly customizable designs, making it easier to tailor workstations to specific roles and ergonomic needs. Adjustable heights, built-in storage, and accessory integration create a workspace that reduces strain on workers while improving overall efficiency.
Ergonomics play a huge role in lean manufacturing by reducing fatigue and injury risk. With aluminum framing, workstations can be configured for standing or sitting positions, ensuring that workers remain comfortable during long shifts. Custom attachments such as monitor mounts, lighting fixtures, and tool organizers can also be added to keep everything within reach, eliminating wasted movement and improving workflow.
Durable Surfaces That Resist Wear from Heavy Equipment and Materials
Manufacturing workstations take a beating, especially when dealing with sharp tools, heavy parts, and constant use. Standard tables can develop dents, scratches, or even structural weaknesses over time. Aluminum framing paired with durable work surfaces provides a long-lasting solution that holds up against the toughest factory conditions.
Unlike traditional wooden or particle board surfaces that degrade quickly, aluminum-framed tables can support high-impact tasks without showing signs of wear. Many setups also include reinforced surfaces made of high-pressure laminate, stainless steel, or anti-static materials, offering additional durability for specialized manufacturing environments. This combination ensures that workstations remain in top condition even under the most demanding workloads.